Typical cleanrooms consume a lot of energy, anywhere between 2 and 50 times more than what’s consumed by non-classified areas, although this depends on your industry and specific application. This means using a cleanroom for your critical processes will result in a larger carbon footprint for your organisation.
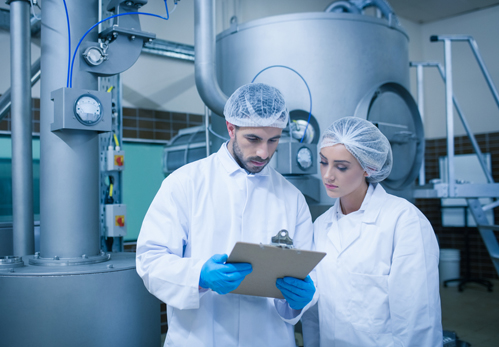
The higher the cleanliness levels of your facility, the higher the energy consumption.
Fortunately, with modern cleanroom technology and the expertise of professionals like Saakvee, your cleanroom can achieve more efficient energy consumption and greener operations. Achieving this will help your organisation’s operations be more aligned with current international cleanroom standards. It can also be a big boon for your company’s public image.
Modular Cleanroom Benefits
- Modular Construction
- Quick Assembly Time
- Versatility
- Reconfiguration
- Airflow Control
- Inexpensive Modifications
Specific guidance on minimising energy consumption in cleanrooms is available in the British standard BS 8568:20131. But to properly apply the provisions of this standard and similar ones, it is necessary to have a clear understanding of energy consumption best practices, especially with regards to reducing Air Change Rates (ACRs).
Energy Saving Methods
Energy saving methods can be specific to some cleanrooms and/or general (applicable to all types of cleanrooms).
Typically, general methods are aimed at:
- Providing heat isolation to buildings and reducing heat gain/losses
- Facilitating air recirculation with minimum outdoor air
- Locating the controlled environment in climate zones where high power is not required in winter/summer
- Preventing unneeded narrow tolerances for temperature and humidity
- Utilising energy efficient ventilators, AHUs and chillers
- Utilising equipment (filters, HVAC units, etc.) with reserve power. This is because larger nominal power consumes less energy
- Removing excess heat load from process equipment with the aid of in-built mechanisms.
Cleanroom Design, Build & Validation
- Budgeting and planning
- Engineering, design & layout
- Airflow and filtration design
- Construction and Installation
- Full Certification of our product
- Industry-specific equipment installation
- Validation
Specific methods on the other hand are generally aimed at cleanroom features. Examples are:
- Making the cleanroom as small as possible
- Reducing the number of personnel with access to the cleanroom by using more technologies that don’t require people
- Avoiding overly focusing on the cleanroom’s class of cleanliness
- Sealing all leaks
- Avoiding over-specification of Air Change Rates and recovery time
- Using HEPA filters with reduced pressure drop
- If a process requires maintenance of higher cleanliness class in a limited area, local protection is to be used
- Paying close attention to garments, training, operation, hygiene, and so on
- Minimising air flow rate when ‘at rest’
- Figuring out specifically required air flow rates during operation and testing, then using the data from this to set the ACR
Modular Cleanroom Services
- Design & Build
- Free Site Survey
- Free Design Service
- Cleanroom Planning
- Construction and Installation
- CNC Engineered
- Training & Support
- Discounted Service Contracts
- Remedial Works
- Panel Repairs
- Alternations
- BMS Management
- Cleanroom Certification
- Differential Pressure Qualification
- Servicing Testing Validation
- Smoke Testing
- DOP Testing
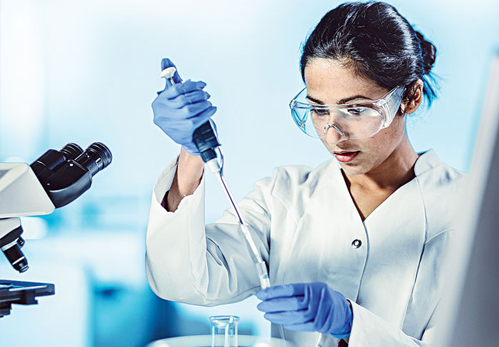
The consumption of energy in a cleanroom will vary between cleanrooms with unidirectional and non-unidirectional flows.
In cleanrooms with unidirectional air flow, air velocity is the key factor. Non-unidirectional air flow cleanrooms on the other hand have ACR as the key factor. ACR needed in a cleanroom will depend on a variety of factors such as the removal of heat loads, the volume of outdoor air needed for breathing, maintaining pressure difference the compensation of local exhausts and achieving desired cleanroom class. These should be factored in during the design stage of the cleanroom.
Cleanroom Features
- GMP
- ISO 4-9
- ISO 14644
- Low Power Consumption
- Environmentally Friendly
- HEPA Filters
- Air Filtration
- Fan Filter Units
- Cleanroom Ceiling System
- Temperature Control
- Access Control
- Inter Lock Door Systems
- Air Showers
- Unidirectional Airflow
- Desiccator Cabinets
- Horizontal Flow Wall Modules
- Horizontal Laminar Flow Clean Benches
- Laminar flow cabinets
- Laminar Flow Canopy
HVAC systems with high air flow to supply the required ACR consume large amounts of energy because the non-unidirectional (turbulent) air flow places a high burden on the heating, air ventilation, cooling, and humidification system.
Reducing the frequency of air changes in a cleanroom is referred to as “Turning Down”. The more frequently air is changed per hour, the cleaner the cleanroom. Cleanrooms are rated on a scale of 1 to 9 by the International Organization for Standardization (ISO). ISO-9 has the most particles per cubic foot while ISO-1 has the least. The ideal ISO standard of a cleanroom is typically determined by the purpose of the cleanroom.
An ISO-6 cleanroom may need 90 air changes each hour, while an ISO-7 cleanroom needs 60 air changes per hour to reach its prescribed particle count. To achieve a higher standard of cleanliness, frequency of air change in the cleanroom will have to increase by up to 50% air changes per hour.
With efficient air filters, frequency of air changes or amount of power consumed during air changes can be significantly reduced.
Cleanroom Industries/Sectors
Contact Saakvee Today To Lower Power Consumption Of Your Cleanroom
In truth, most cleanrooms don’t need to meet higher ISO standards, but, we can help reduce your cleanroom’s power consumption through:
- Designing your cleanroom around direct current fan filter units. We can also incorporate design features that compensate for operational factors that increase energy use.
- Providing you with a more energy efficient cleanroom, such as our state of the art Modular cleanrooms
- Reducing number of air changes
- Run equipment such as fans on an alternating basis to reduce power consumption as well as wear and tear.